PTA HARDFACING
THE PLASMA PROCESS
Plasma derives its unique operating characteristics from the unique torch design. As in TIG welding, the arc is formed between the end of a tungsten electrode and the workpiece . However, in the plasma torch, the electrode is positioned behind a copper nozzle with a central orifice. Plasma is present in all arcs. If a constricting orifice is placed around the arc, the amount of ionization , or plasma , is increased. This results in a higher arc temperature and a more concentrated heat pattern than exists in TIG welding. Plasma torch designs exist for various applications like cutting , welding , hardfacing, cladding, spraying , melting , heating etc. This articles discusses the use of a special adaptation of the plasma welding torch for hardfacing .
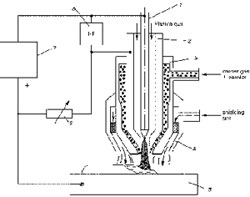
|
- Electrode;
- Plasma nozzle;
- Powder feed nozzle;
- Shielding nozzle;
- Work piece;
- Ballast resistance;
- Power source;
- Oscillation unit.
|
Schematic illustration of the PTA system : |
|
PTA (Plasma Transferred Arc)
Plasma Transferred Arc System (PTA) is a high energy, inert gas welding process. Ar is basically used for arc plasma supply, powder transport and molten material shielding. It produces a very high quality deposit offering optimal protection with minimal dilution or deformation of the base material. It is a process that deposits very precise coatings of perfectly controlled alloys on mechanical parts that are subject to intense wear, significantly extending their service life.PTA technology is particularly effective in protection against corrosion, thermal shock and abrasion. A wide range of overlay alloys is available for practically any part. Some alloys are very hard, others are softer with hard abrasion-resistant particles dispersed in a text-small-link. Certain alloys are made to rebuild a part to a required dimension while others are designed to be a final overlay that protects the work surface.
BENEFITS OF HARDFACING:
- Reduces Cost: Restoring a worn part to "as new" condition generally costs between 20-70% of a brand new replacement part.
- Prolongs Equipment Life: Service life increases of 3 to 10 times are common with properly overlaid parts.
- Reduces Downtime: Parts last longer and fewer shutdowns are required.
- Less Spare Parts Inventory: There is no need to keep numerous spare parts when worn parts can be rebuilt.
|
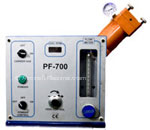 |
Power Source, Control Panel, Oscillator & Turntable |
Powder Feeder & Plasma Torch |
TYPES OF WEAR CONDITIONS HARDFACING CAN REDUCE OR ELIMINATE:
Abrasive wear is caused by foreign materials rubbing against a metal part.
Metal-to-metal wear results from non-lubricated friction of metal parts. As metal surfaces slide against each other, the high areas are broken and tiny fragments of metal are torn away.
A blow or a series of blows to a surface resulting in fracture or gradual deterioration. In general, impact resistance
decreases as carbide content is increased. Because abrasion resistance increases with carbide content, a compromise often must be made.
Heat influences wear resistance by:
- softening the metallurgical structure.
- causing a phase change that increases hardness and brittleness.
- allowing chemical attack leading to galling and deterioration.
The deterioration of metal by chemical or electrochemical reaction with its environment.
Wear in which loss of material occurs due to the cutting action of moving particles carried in a fluid stream is termed impingement erosion. At low impingement angles (<15%), hardfacing with large amounts of carbides (hypereutectic alloys), are recommended. At high impingement angles (>80%), large amounts of text-small-link (hypoeuctectic alloys), are recommended.
Material loss due to very-small-amplitude vibrations at mechanical connections, such as riveted joints. This type of wear is a combination of oxidation and abrasive wear.
PTA HARDFACING PROCESS
|
Torch Mounted on Oscillator |
The PTA welding system can deposit metal alloys on metal surfaces at rates of up to 20 lb/h . The system can be fitted with automated manipulators to handle different parts, even those with complex shapes and narrow tolerances
The PTA system works with different metal powders as filler material, such as chrome carbide, tungsten carbide, and nickel- and cobalt-based powders. Future development could also see the use of ceramic-based powders. Using these hard-wearing materials can improve the durability of the weld.
When used to deposit powder metal alloys on a substrate, the PTA system has a dilution level of 3 to 7%. Compare this to submerged arc systems, which can dilute the base metal by as much as 40%. Combined with a narrow heat-affected zone, the PTA system's low dilution rate prevents undesired substrate changes and can enhance the alloy's wear performance in applications for manufacturing wear components. It also results in a smooth surface finish for easier and quicker finishing and machining.
THE EFFECT OF DILUTION:
The welding heats required for proper application of hardfacing materials are not necessarily the same as those required for structural welding. Instead of producing an admixture of two compatible metals, as in structural welding, PTA provides a bead or a surface deposit of alloyed metal located to resist impact or abrading action. The process requires only sufficient application heat to obtain a sound bond with the parent metal. Admixtures of the two metals are minimized.
Using too much heat during hardface welding will dilute the hardface alloys with the base metal, thereby reducing effective wear resistant properties of the material.
Excessive heats will vaporize the alloys and will cause oxidation. Overly heated weld puddles can further result in
such fluid condition of the alloys that they create a thinner deposit than may be intended. Insufficient welding heat, on the other hand, will cause insecure bonds with the base metal and can possibly result in spalling. A cold weld deposit, especially when applied to chilling metal, will often cool rapidly enough to create shrinkage, more commonly called "cold checks." Such fractures can also result in eventual spalling of metal.
APPLICATIONS
In a competition with laser surfacing the PTA technology offers much more high productivity, comparable high quality of deposits and significantly lower costs.
Typical application areas of the PTA technology are extruding machine screws, valves, valve seats of internal combustion engines (motorcar, marine, locomotive etc.), accessories for ships, petroleum chemistry and power generation, cutting tools (milling cutters, broaches, knifes) ,Equipment for mining, crushing, rolling, road building and tunneling, Process equipment in ceramics and cement production,Molds and forging dies, Pulp and paper industry equipment, Agricultural equipment, parts for nuclear plants, parts for chemical plants
SUMMARY
|
P.T.A. DEPOSITS SHOW THE FOLLOWING CHARACTERISTICS:
- An attractive bead with no signs of oxidation, and with little or no ripple.
- Very low dilution
- High, density, no porosity & no inclusions.
- Microphotos or x-rays show the deposits to be of high density & metallurgically bonded to the Substrate.
|
|